Six Sigma is a data-driven approach for eliminating defects and waste in any business process. You can compare Six Sigma with turning your water faucet and experiencing the flow of clean, clear water. Reliable systems are in place to purify, treat, and pressure the water through the faucet. That is what Six Sigma does to business: it treats the processes in business so that they deliver their intended result.
Our Lean Process and Six Sigma workshop will provide an introduction to this way of thinking that has changed so many corporations in the world. This workshop will give participants an overview of the Six Sigma methodology, and some of the tools required to deploy Six Sigma in their own organizations.
Module One: Getting Started
Module Two: Understanding Lean
Module Three: Liker’s Toyota Way
Module Four: The TPS House
Module Five: The Five Principles of Lean Business
Module Six: The First Improvement Concept (Value)
Module Seven: The Second Improvement Concept (Waste)
Module Eight: The Third Improvement Concept (Variation)
Module Nine: The Fourth Improvement Concept (Complexity)
Module Ten: The Fifth Improvement Concept (Continuous improvement)
Module Eleven: The Improvement Toolkit
Module Twelve: Wrapping Up
In this Practical, Lean Process & Six Sigma Training, you would learn to
- Develop a 360 degree view of Six Sigma and how it can be implemented in any organization.
- Identify the fundamentals of lean manufacturing, lean enterprise, and lean principles.
- Describe the key dimensions of quality – product features and freedom from deficiencies
- Develop attributes and value according to the Kano Model
- Understand how products and services that have the right features and are free from deficiencies can promote customer satisfaction and attract and retain new customers.
- Describe what is required to regulate a process
- Give examples of how poor quality affects operating expenses in the areas of appraisal, inspection costs, internal failure costs, and external failure costs
- Using basic techniques such as DMAIC and how to identify Six Sigma Projects
- Use specific criteria to evaluate a project
- Discover root causes of a problem
Anyone can attend who wants to improve the Lean, Six Sigma Process for continuous improvement. No specific skills or pre-requisites.
You must have basic knowledge of the English language.
Best suited for individuals, as well as employees in Sales, Marketing, Customer Service, Purchasing, IT, HR, Finance, Manufacturing, Data Analysis, and other departments in companies who want to setup and implement a Lean, Six Sigma Process in their organization.
From Individual contributors, to supervisors, team leaders, executives, managers, and directors, every one needs to increase profits by eliminating variability, defects and waste.
In this Practical, Lean Process & Six Sigma Training, you would learn to
- Develop a 360 degree view of Six Sigma and how it can be implemented in any organization.
- Identify the fundamentals of lean manufacturing, lean enterprise, and lean principles.
- Describe the key dimensions of quality – product features and freedom from deficiencies
- Develop attributes and value according to the Kano Model
- Understand how products and services that have the right features and are free from deficiencies can promote customer satisfaction and attract and retain new customers.
- Describe what is required to regulate a process
- Give examples of how poor quality affects operating expenses in the areas of appraisal, inspection costs, internal failure costs, and external failure costs
- Using basic techniques such as DMAIC and how to identify Six Sigma Projects
- Use specific criteria to evaluate a project
- Discover root causes of a problem
Best suited for individuals, as well as employees in Sales, Marketing, Customer Service, Purchasing, IT, HR, Finance, Manufacturing, Data Analysis, and other departments in companies who want to setup and implement a Lean, Six Sigma Process in their organization.
From Individual contributors, to supervisors, team leaders, executives, managers, and directors, every one needs to increase profits by eliminating variability, defects and waste.
Module One: Getting Started
Module Two: Understanding Lean
Module Three: Liker’s Toyota Way
Module Four: The TPS House
Module Five: The Five Principles of Lean Business
Module Six: The First Improvement Concept (Value)
Module Seven: The Second Improvement Concept (Waste)
Module Eight: The Third Improvement Concept (Variation)
Module Nine: The Fourth Improvement Concept (Complexity)
Module Ten: The Fifth Improvement Concept (Continuous improvement)
Module Eleven: The Improvement Toolkit
Module Twelve: Wrapping Up
Anyone can attend who wants to improve the Lean, Six Sigma Process for continuous improvement. No specific skills or pre-requisites.
You must have basic knowledge of the English language.
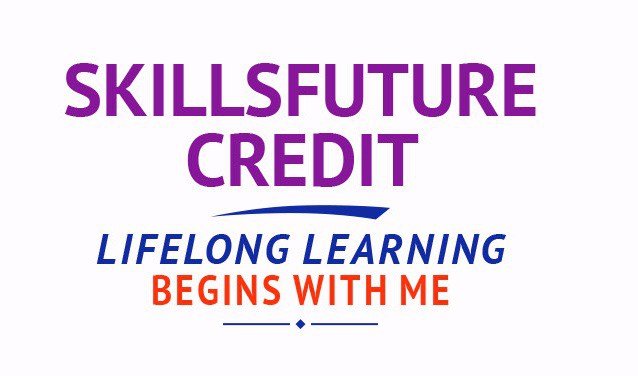
SkillsFuture Ready
Singaporeans can use $500 SkillsFuture Credits for this training to offset the course fees.
Contact us for advise on how to go about claiming your SkillsFuture.
Get Started Today!
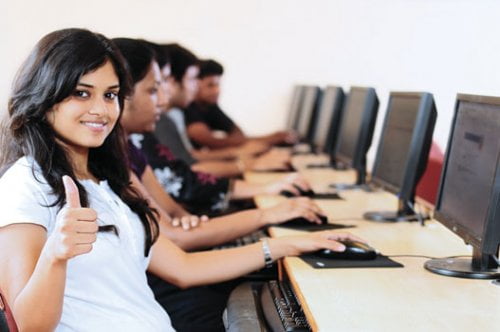
Learn By Doing
You learn best when you Do It Yourself.
We teach you, step by step, how you can learn new skills, build your knowledge and enhance your career prospects quickly & easily, with Practical Tips & Tricks!
Do You Have Any Questions or Need a Quotation?
Simple. Just tell us what you need. We’ll be glad to help you!
Some of the companies that experienced our trainings
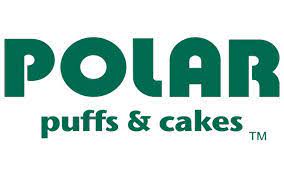
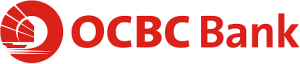
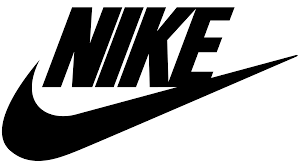
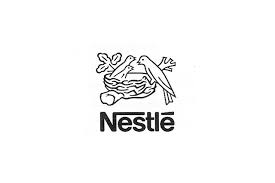
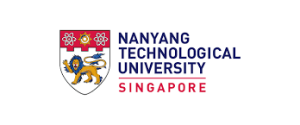
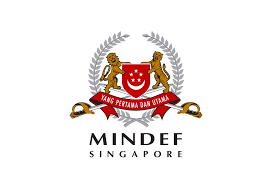
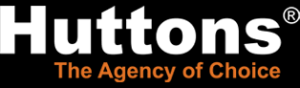
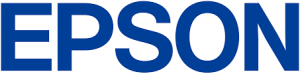
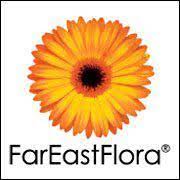
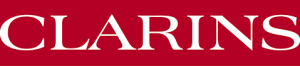
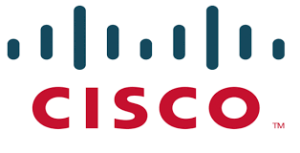
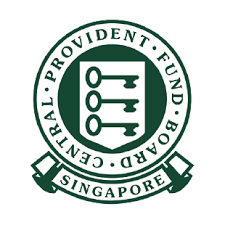
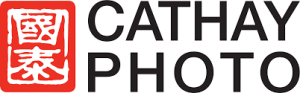
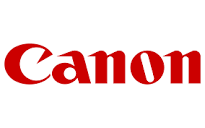
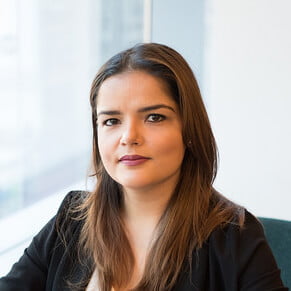
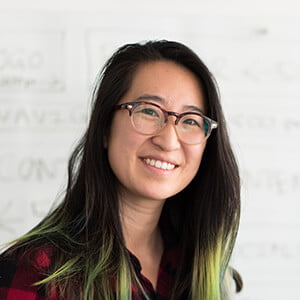
How To Register
Register for the 1 Day Lean and Six Sigma Workshop Training today by simply clicking on the chosen course date available at the top of this page.
Need Help?
- Call us at +65 6250-3575, SMS / WhatsApp: +65 9066–9991
- Send an email to training@intellisoft.com.sg OR
- Submit an online enquiry if you have any questions regarding Lean and Six Sigma Workshop.
We also offer Corporate Trainings for Lean and Six Sigma Workshop.
This program can be customized according to your needs and can be conducted in house if you have a group of more than 8 people. For more information you can call us at +65 6250-3575 Email to training@intellisoft.com.sg